High Performance Sedimenter Centrifuge-GCF-
SD-G455BF/DS
The G-Centri-Force Engineering P Ltd High-performance SD-G455Sedimenter centrifuge provides the most cost-effective solution available on the market for various Solid-Liquid Separation plants. G-Centri-Force Sedimenter centrifuges are designed for food and beverage applications where good hygiene practices are essential in order to comply with strict sanitary regulations. These Sedimenter centrifuges are available for both 2-phase with High G-Force were separate micro solids particles form liquid. They are ideal for use in the food industry in situations where the material being processed has to be separated into both a liquid and a solids phase, or into two liquid phases and a solids phase. The SD-G455range provides the most cost-effective, high-performance solution combined with the lowest power consumption and life cycle costs available within the process industries., with both very low (<1%DS) and very high solids contents. Whether you require lower life cycle costs, higher cake dryness driven by 2/3 stage planetary gearbox. G-Centri-Force Sedimenter centrifuges provide design options such as grooves in the bowl to provide a more hygienic way to transport the material being processed through the unit. Other options include a paring disc and a complete purge system to keep foaming to a minimum and limit oxidation; pulp wash facilities; process rinse and a full cleaning-in-place (CIP) capability, as well as FDA-approved elastomers and seals.
Application Area
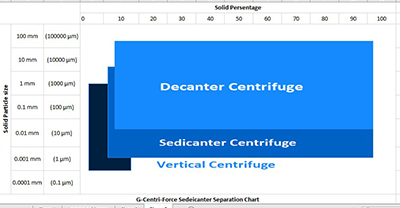
The Sedimenter has turned out to be the best solution compared to other industrial centrifuges when it comes to separating high-concentration fine and soft solids from suspensions. Sedimenter are reliably used in the following applications:
Comparison of application areas for Sedimenter, decanters and Vertical Centrifuges depending on particle size and solids concentration in the feed
Efficiency performance chart
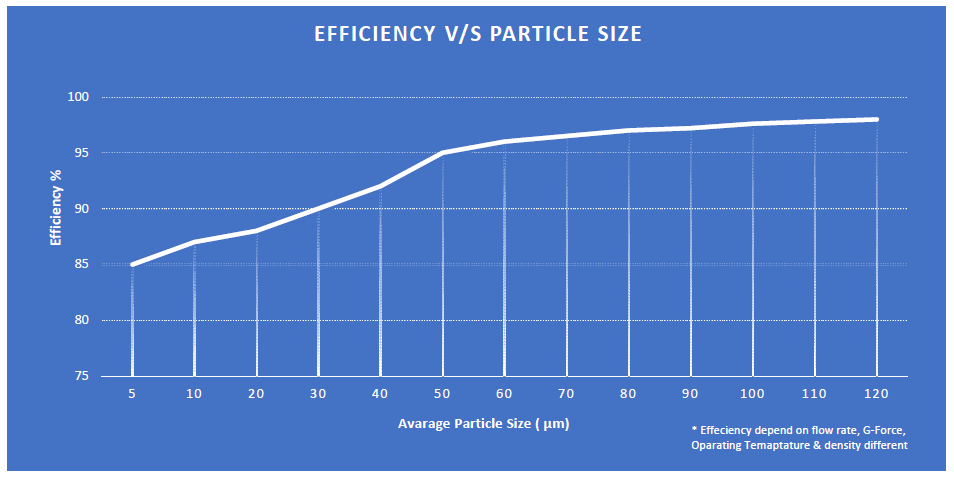
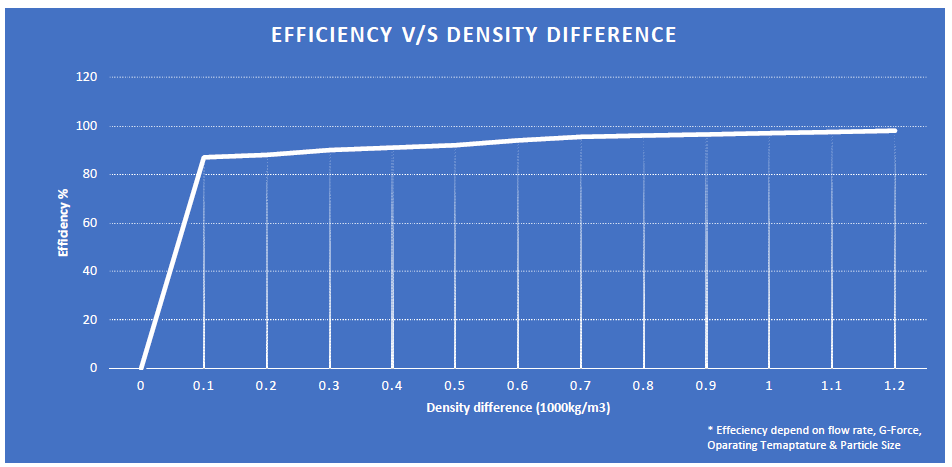
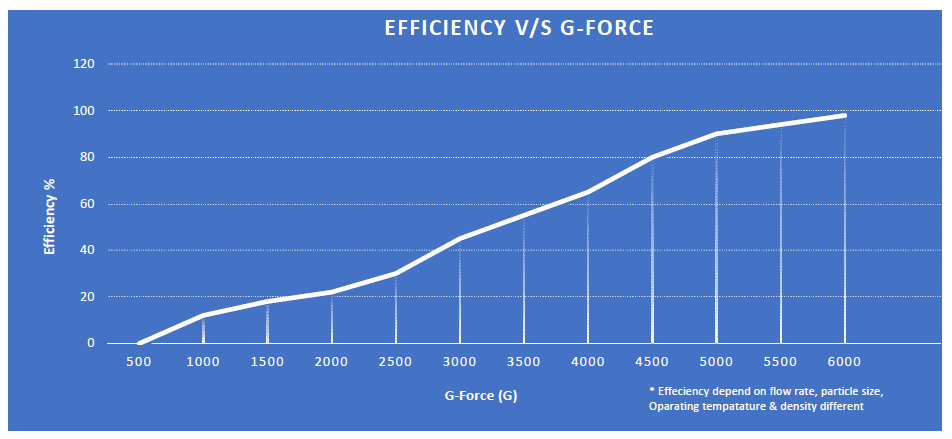
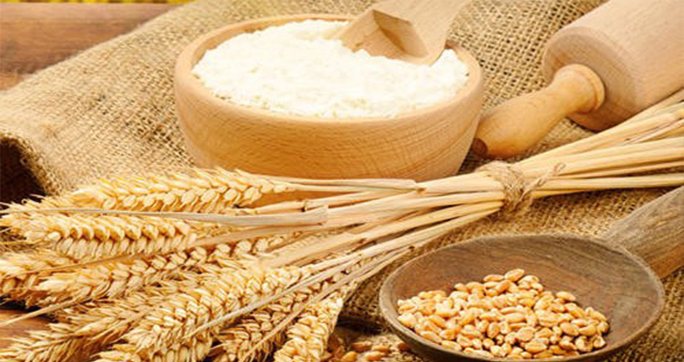
Wheat Starch:
In the production of wheat starch, the Sedimenter separates undissolved particles from the pentosan phase. Fine starch can be recovered from different process stages. Thus, it is possible to increase the product yield. The quality of the process water is improved.
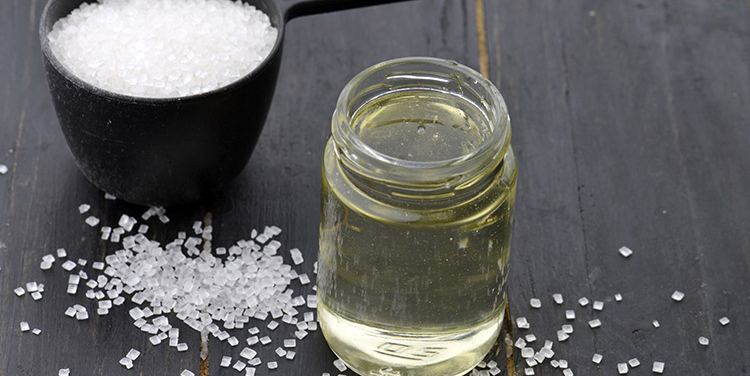
Sugar Syrup:
In the production of wheat starch, the Sedimenter separates undissolved particles from the pentosan phase. Fine starch can be recovered from different process stages. Thus, it is possible to increase the product yield. The quality of the process water is improved.
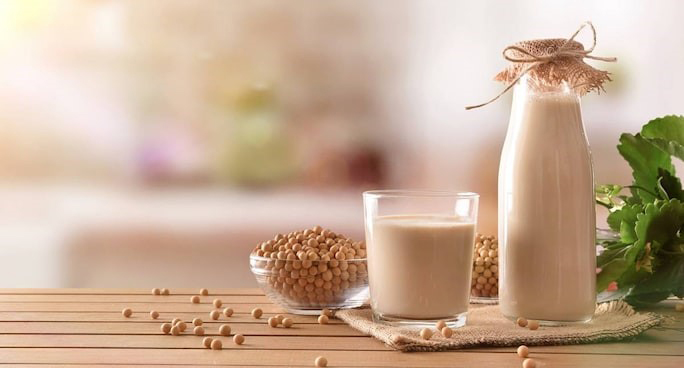
Soya Milk:
Soya and protein yields can be increased. Especially in combination with fine product grinding, it is possible to optimize the production process.
.jpg)
Plant Extraction:
The Sedimenter increases the yield of different plant extracts, even in case of very fine maceration. The extraction medium can be water or a solvent.
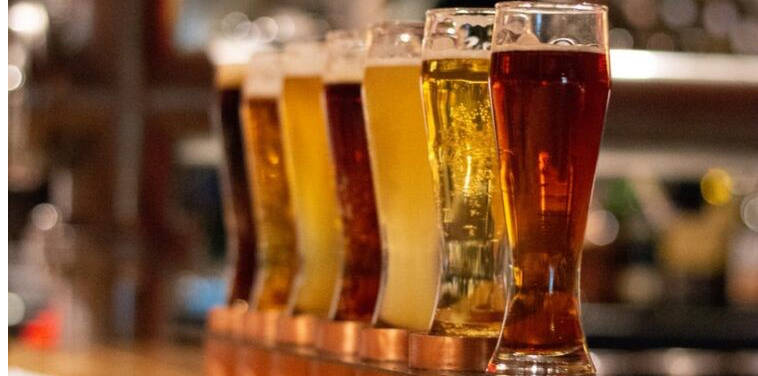
Beer Recovery:
The Sedicanter efficiently thickens surplus yeast generated in the brewing process, creating two valuable products: The recovered beer can be reintroduced into the brewing process and the yeast can be used for further processing in the food industry, in the dietary supplement industry, or as animal feed
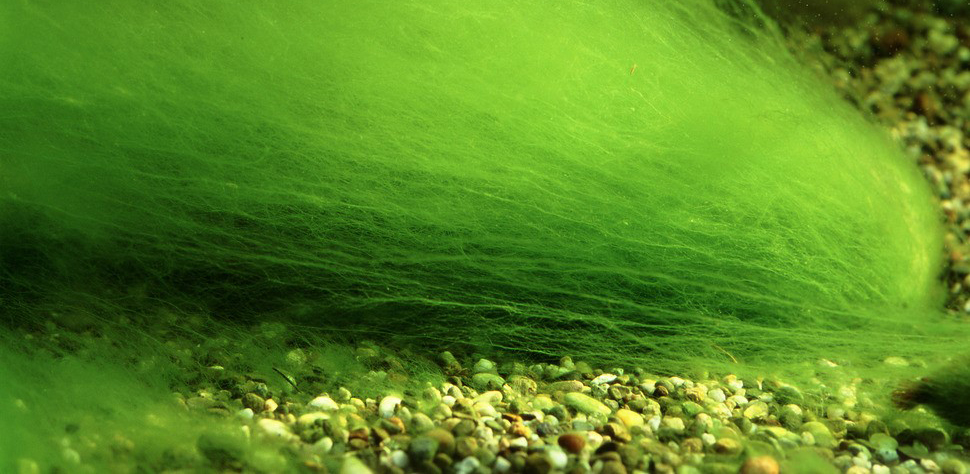
Algae:
Pre-concentrated algae are thickened and/or dewatered. That means that the energy efficiency of the harvesting process is improved since the algae comes out as a compact cake. Therefore, only a small quantity of water has to be separated in the subsequent process stages.
Alcohol Stallage:
The Sedimenter can be used for separating further solids of the so-called thin stillage (after first separation). This means that the selective protein yields from thin stillage increase.
Biomass & Broth Technology:
Efficient separation of biomass from fermentation broth is one of the focus applications of the Sedimenter. It is used in industrial biotech- nology for the production of vitamins and enzymes.
Advantages of the G-Centri-Force Sedimenter
Efficient separation of suspensions for which decanter centrifuges or disk stack centrifuges provide only in- sufficient results Processing of suspensions with fine and pasty solids or fluid sediments (yeast, protein, etc.) High g-forces for efficient solids separation and maximum clarification of the liquids, similar to disk stack centrifuges
The SD-G455 feature set follows in the path of the other Sedimenter centrifuges in the SD-G455 series range, with
- Fully Auto & Manually
- Chemical related Critical parts made of wear-resistant material
- High performance combined with low energy consumption.
G-Centri-Force Sedimenter centrifuge with a focus on hygiene, reliability, easy access and low noise levels. The rotating assembly is mounted on a compact welded box beam frame with main bearings at both ends. The cover is hinged to enable easy access for inspection, cleaning and maintenance. The in-line motor is mounted on the Sedimenter with adjustable brackets to make it easy to adjust belt tension. The bowl is driven at the inlet end by an electric motor and V-belt transmission. The bowl, conveyor, casing, inlet tube, outlets and all other parts in contact with the process media are made of AISI 316 stainless steel.
Benifits
- Reduces sludge volume
- Cost-effective performance
- Continuous operation
- Compact, modular design
- Star-Delta operating or PLC base.
Working Principle
Separation takes place in a horizontal conical bowl equipped with a screw conveyor. The feed enters the bowl through a stationary inlet tube and is accelerated smoothly by an inlet Discharge at smaller end of bowl. Centrifugal forces cause
Sedimentation of the solids on the wall of the bowl. The conveyor rotates in the same direction as the bowl, but at a different speed, thus traveling the solids along with the liquid together towards the bigger conical end of the bowl. Only the driest fraction of the cake leaves the bowl through the solids discharge openings into the casing. Separation takes place throughout the total length of the conical section of the bowl, and the clarified liquid leaves the bowl by flowing over adjustable plate dams into the casing. The separated liquid transfer to large end side using centripetal pump.
Main Drive system:
The bowl is driven by an electric motor and a V-belt transmission drive. Sedimenter start by Star-Delta mode, but in special case used VFD drive.
Conveyor Drive system:
Conveyor drive by extra electrical motor true 2 stage high speed planetary gearbox design & pretend by G-Centri-Force Engineering P Ltd. The Conveyor driven by an electric motor direct transmission drive. This conveyor drives motor start by VFD method.
Design- Options:
G Series BF Sedimenter centrifuges provide design options such as grooves in the bowl to provide a more hygienic way to transport the material being processed through the unit. Other options include pulp wash facilities, process rinse and a full cleaning-in-place (CIP) capability, as well as FDA-approved elastomers and seals. ATEX-compliant Sedimenter are available for zones 1, 2 and 22. Gastight Sedimenter are available for processing flammable feed. A compact, in-line frame carries the rotating part with main bearings at both ends. Vibration isolators are placed under the frame. The rotating part is enclosed in a casing with a co+ ver and a bottom section in which the solids and liquid outlets are integrated. All G455 Sedimenter centrifuges are available in 2-phase versions and can be Hygienic compliant. Sedimenter centrifuge will be provided with Espey Seals for sealed Sedimenter.
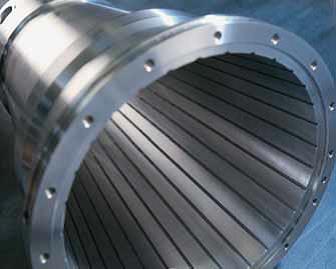
CIP (Cleaning-In-Place)
The Graphic Presentation of the cleaning procedure is meant as a suggestion, different processes will require specific cleaning cycles. Lye detergents and other cleaning agents used for cleaning already existing stainless-steel plant parts are normally also applicable in the wash cycles for the G-455BF Sedimenter.
Separate, automated CIP stations are available on request if there is no possibility to connect to already existing systems
-sedimenter.jpg)
Scroll conveyor
Wear protection in the form of food grade hard-surface, combined with cobalt, ensures a service life that is at least double that of the standard configuration.
Feed zone and solids outlet
The new design for both the feed zone and solids outlets results in a significant increase in solids handling capacity.
The full-flow feed zone design ensures a high hydraulic throughput with no blockages or feed rejection.
The wear-prone areas of the feed zone and solids outlet are protected with easily replaceable, hard-surface inserts. The 360-degree solids outlet configuration ensures availability of the maximum solids discharge area.
Materials
The bowl, conveyor, inlet tube, outlets, cover, and other parts in direct contact with the process media are made of AISI 316 and Both Side Hubs & bowl conical made by High strength Duplex Stainless Steel. The discharge ports, conveyor flights and feed zone are protected with highly erosion resistant materials. The frame is made of mild steel with an epoxy paint finish.
Optimization
The G range of Sedimenter centrifuges can be adjusted to suit individual sludge dewatering and thickening needs. You can obtain maximum separation efficiency by first varying the feed rate, rotational speed, and polymer type and dosage. The optimal balance between liquid clarity and solids dryness is achieved by varying the differential speed between the conveyor and bowl and the pond depth in the bowl.
PLC Controls Package:
Each SD-G455 Sedimenter centrifuge is equipped with a PLC control package as standard, pre-installed and Factory tested. The combination of PLC control systems and SD-G455 separation technology makes sure you get the most out of any SD-G455 installation, at the same time as keeping costs for installation, commissioning, operation and maintenance to a minimum. Additional enhancement packages are available for the PLC controls package.
Automatic Grease Lubrication
In contrast to the manual central lubrication system, the greasing system can be operated automatically. This ensures uniform and reliable lubrication of the centrifuge. It prevents bearings from being under or over-lubricated and eliminates short-term spikes in bearing temperatures and excessive grease consumption. The function of the grease pump is controlled by the control system. For the most stringent requirements, an oil-air lubrication system can be provided by additional cost.
Central Lubrication System
Lubrication from a central manually operated pump. The lubricant is accurately dispensed through a piston distributor to the designated greasing points.
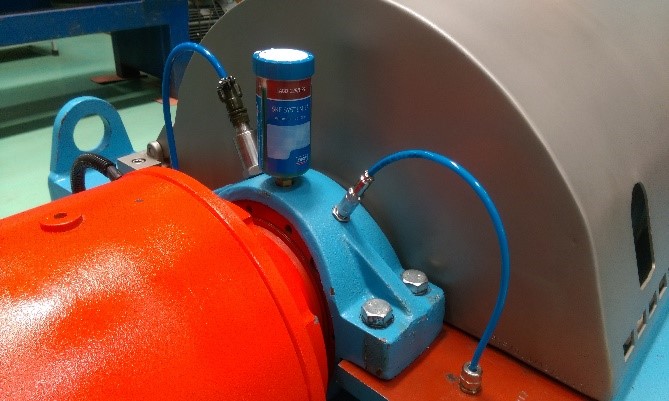
Vibration Monitoring:
Vibration sensors transmit acceleration signals to an analyzer that sounds an alarm or shuts the centrifuge down upon reaching the maximum permissible level.
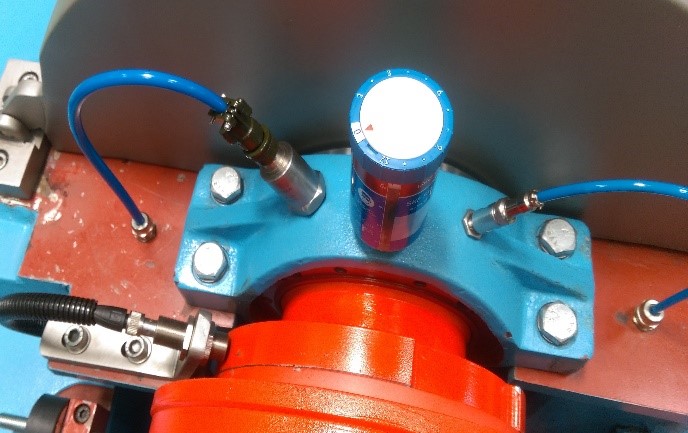
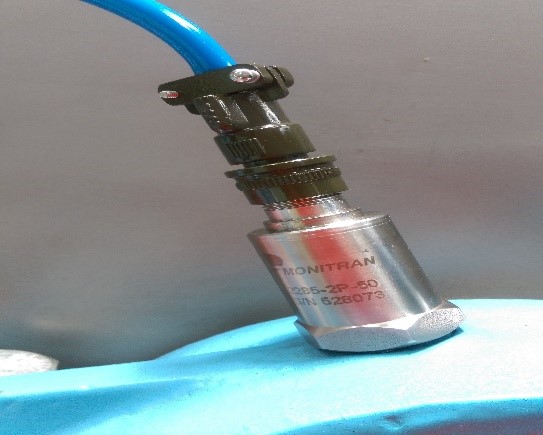
Speed Monitoring
Bowl speed and scroll differential speed are each measured by an inductive proximity switch and shown on a digital display. Continuous monitoring of maximum and minimum values during operation helps to minimize preventable failures and maintain acceptable safety standards.
Temperature Monitoring
Bearing temperatures are continuously monitored on GCF centrifuges by means of resistance thermometers. Upon exceeding pre-set temperature limits – between 100°C and 130°C depending on the individual application - , the centrifuge gives an alarm or shuts down. This preventive measure safeguards against bearing failure or machine damage.
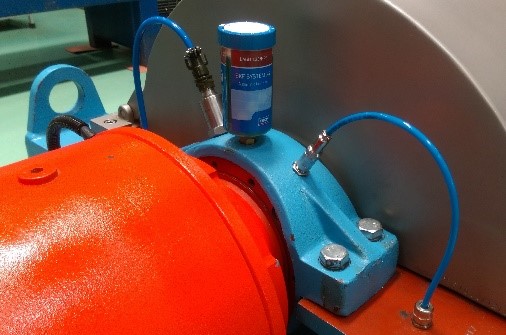
Details Specification
Application | Beverage&Food |
Flow rate | 4-5 M3/ Hours |
Filtrate solids recovery | >90-95 % |
Max Solid Density | 2.3 kg/dm3 | Performance Optimization |
---|---|
Product Temperature | 70-80*C |
Inlet Solids | 2.0-8.0 % w/w suspended solids |
Recovery | 85-95% solids will be settle having following particle size distribution at primary stage |
>10 Microns Nil | |
<10 but >20 Microns 20% | |
<20 But >90 Microns 90% | |
<80 Microns Nil | |
80-85% solids will be settled assumption that the process is of standard type. | |
Performance | Performance is fully dependent upon back set ratio, type of solids, solid particle size, temperature, and other process conditions. Presence of abrasive particles such as sand in the feed to decanter will increase the wear and tear of the conveyor & discharge wear bush. |
General information
Design | Co-Counter Current |
Typical application | Recovery fine micro level solids from liquid |
Max. Design temp. | 100 Degree Celsius |
Min. Design temp. | 0 Degree Celsius |
Centrifugal G-ratio | 6000 G |
Total Length | 4348 mm |
Total Width | 1067 mm |
Total Height | 934 mm |
Total Weight | 3260 Kgs |
Bowl Shell Assembly
Bowl Shell Type | 2 Phase Separation |
Bowl Shell Diameter | 455 |
Total Shell length | 1553 mm |
Material of Shell & Hubs | Duplex 2205 |
Liquid outlet type | 6 plate dams or Centripetal Pump liquid discharge |
Liquid outlet radius | 135 mm |
Solid outlet type | Discharge Port |
Solid outlet radius | 133 mm |
Taper cone | 3* & 50* |
Max. bowl Shell speed | 5000 rpm |
Working bowl Shell speed | 4500 to 5000 rpm |
Screw Conveyor assembly:
Conveyor design | ‘Y’ Type Single cone |
Type of conveyor | Standard with Tungsten+Nikel base Spray powder hard-surfacing of Half-length Conveyor |
Feed zone design | ‘Y’ Type |
Material | Duplex 2205 |
Pitch | 1 X 140 mm |
Beach Cone Angle | 3* & 50* |
Base Frame
Type | Box beam profile |
Material | Mild steel for Base Frame AISI304 for base Frame |
Sludge outlet area | Wear plate AISI 316 |
Casing assembly
Type | Top Cover |
Material | AISI 316 |
Sludge outlet area | Replaceable Wear plate |
Gear-box
Gearbox type | Planetary - Two stage |
Gearbox ratio | 1:97 |
Gearbox Model | G-97-3 |
Lubrication | Special Oil |
Back Drive
Main motor size | 7.5KW/ 10HP |
Motor type | 3 phase, 2 pole, 2880 rpm (syn) |
Motor data | 415 V / 50 Hz |
Motor Protection | Class F IP 54 |
Mounting | Flange Mounted |
Starting | VFD controlled |
Transmission | Drive with Timing Belt & Pulley |
Main Drive
Main motor size | 30KW/ 40HP |
Motor type | 3 phase, 2 pole, 2880 rpm (syn) |
Motor data | 415 V / 50 Hz |
Motor protection | Class F IP 54 |
Mounting | Flange Mounted |
Starting | VFD controlled |
Motor pulley | Taper Lock Fix pulley |
Transmission | V Belt |
Electrical
PLC control With Main & Back Drive motor & VFD | |
Interlocks (Stop Sedimenter motor + signal to feed pump motor) | Motor protection be Overload & Temperatures Conveyor Overload by VFD Interface
Cover Open (Limit switch) Speed for Main & Sun-wheel with differential Lubrications System Vibration Monitoring Temperatures Monitoring On field & on panel Emergency stop switch |
Panel Details | MS Fabricated with Canopee Size: 1000(W) X 1500(H) X500( D) Powder coated RAL-7035 with IP 65 protection. |
Cooling System | |
Power Supply | Input power KW380-440 VAC ,50/60HZ,3PH. |
System Details | PLC – Siemens make PLC system with 9’’ HMI 20 digital inputs, 16 Digital output, 4 analog Input, 2 Analog outputs for temp. sensor & 2 Analog output for Vibration sensor
VFD - ABB makes ACS 880 for main & back drive motor Protocol – Ethernet Switchgear – all switchgear are SCHIENDER make Sensors – 2nos RPM sensors PEPPERL+FUCHS make for bowl & conveyor speed, 2nos of Vibration sensor range 0-50mm/sec, 2nos of TEMP sensors G-Centri-Force make |
Signal Interface | Customer takes all read parameters from centrifuge system by ETHERNET |
System Alarm | Conveyor Overload, EMG stop on field & on panel, Main Drive overload/trip, Main Motor over TEMP, Back Drive overload/trip, Back Motor over TEMP, Machine Vibrations high, Solid & Liquid end bearing TEMP high, Cover open |
Cables | Centrifuge to panel 30meter For Main motor size- 4core 16sq/mm, for Back drive motor size-4core 6sq/mm, and control cable size 24core 1sq/mm. The incoming cable size 4core 25sq/mm (in customer scope) Cables with cooper conduits |
Cooling | 0.5kw panel A/C (Optional) |
Spares, Tools & Drawing
Included Spares | 1 set of services kit |
Included lubricants | 1 set of lubricants, grease & gearbox Oil |
Included tools | 1 set of special tools for maintenance |
GA Drawing | Foundation Drawing |
Control panel | Control panel Drawing |
Instruction Manuals | 1 set Sedimenter Operator with Installation, Maintenance & Spares Parts |