Drive System
A decanter centrifuge requires two independent drive systems. The bowl operates at a high rotational speed to create a high g-force. The scroll rotates inside the bowl with a low speed to the bowl (differential speed). G-CENTRI-FORCE applies advanced engineering techniques to accelerate the decanters to high speeds in safe. One of the most important key factors for decanters is the differential speed. Differential speed determines the amount of moisture hold in the separated solids and the clarity of the Centrate.
This speed can be adjusted according to the required product characteristics.
Drive systems which run to determine this speed are given as below:
1.Constant Speed Drive System (fix speed with torque arm)
This technology is developed for applications requiring solid-liquid separation. Separating one mixture with one liquid and one solid with different density in single equipment has simplified. Two Phase Decanter centrifuges have been operating according to the same basic principle since the 19th Century.
The sun-wheel shaft is immobilized by a spring-loaded lever (fix speed with torque arm) resting against a buffer on an operating arm. The arm is fixed on a shaft, the other end of which carries the switching lever. In the operative position this lever is pressed against the upper abutment pin by the compression spring. Increased load on the conveyor will increase the pressure exerted by the small sun-wheel lever on the buffer of the operating arm. If the load is high enough, the switching lever will rock over against the lower abutment sun-wheel pin. This movement releases the switch. The sun-wheel lever can now rotate freely with the gear box, corresponding to zero conveying speed.
The action of the switching lever also shuts down the main drive motor and the feed pump and actuates an alarm signal.
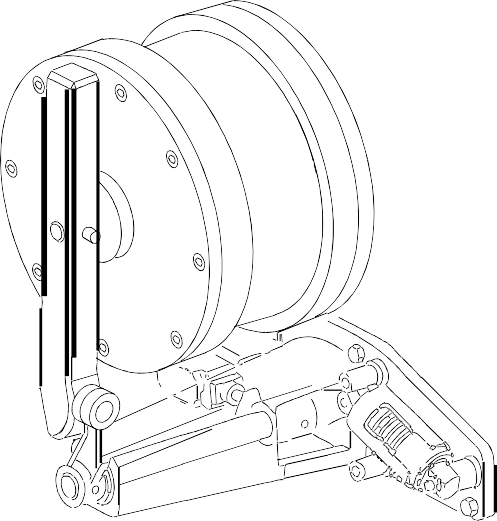
2. Countershaft transmission by G-Centri-Force
The gearboxes an intermediate shaft (lay shaft) is driven from the sun-wheel by use of a belt. Power is transmitted back to the bowl by use of another belt. With this system it is possible to select a variety of differential speeds by changing pulleys and a Share pin/GS coupling protects the decanter against torque overload. They also benefit from the ability to permit some change in the choice of differential by appropriate change of pulley sizes.
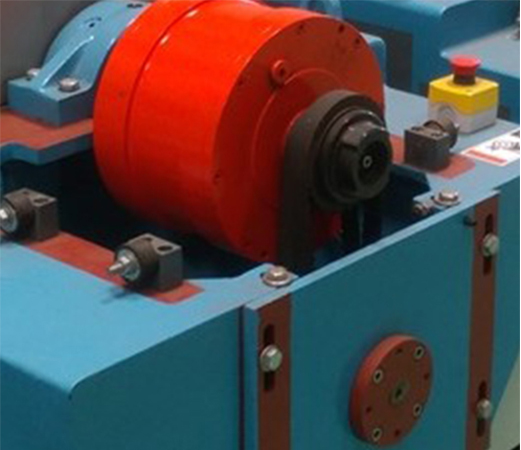
3.Back-drive with AC motor with using VFD
This system is a variant of the AC motor back drive system. The AC motor, equipped with a braking device, facilitates five differential speeds - two by braking the sun-wheel shaft, two driving the pinion shaft, and one with fixed sun-wheel. This system is widely used in the oil field application. A fully regenerative system developed by us is available. The sun-wheel motor is connected to a frequency converter whereby the differential speed can be changed. A second frequency converter is connected to the first one by use of a DC bus whereby it is possible to put the braking power back to the grid when the sun-wheel runs in the same direction as the bowl. Even if the main motor is connected to a frequency converter two dedicated frequency converters for the back-drive are used. The system is controlled by use of the G-Centri-Force* PLC System.
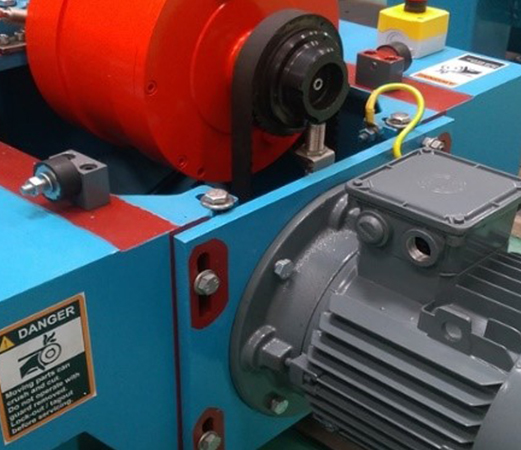
3.Hydraulic back-drive
The main components of the system are a hydraulic pump with variable displacement volume and a pump with fixed displacement volume. A decanter centrifuge requires two independent drive systems. The bowl operates at a high rotational speed to create a high g-force. The scroll rotates inside the bowl with a low speed to the bowl (differential speed).
The scroll and bowl drive of the hydrostatic drive system operate independently from one another in terms of energy and control technology. Torque and differential speed can be controlled according to load and pressure relation. The drives can be directly and infinitely variably controlled, which allows ongoing adaptation to the separating tasks. The fixed displacement pump is connected to the sun-wheel shaft of the gearbox. Thus, the speed of the sun-wheel shaft depends on the oil flow through the pump.
The sun-wheel shaft is made to rotate at a certain speed by the oil flow from the fixed displacement pump. When rotating in the same direction as the bowl the sun-wheel shaft is braked and power is either transmitted back to the bowl via the variable displacement pump and the V-belts, which in that case works as a generator.
A small feed pump mounted on the variable displacement pump provides continuous circulation of oil between the closed circuit and the oil tank. This ensures cooling of the system and a constant minimum pressure.
Overload protection is in three levels. If the decanter cannot scroll itself free by automatically increasing the differential speed, two pressure switches and a relief valve placed in a valve block make sure that:
• The feed pump is switched off when the torque reaches a pre-set level.
• The decanter is stopped if the torque increases further above the pre-set value.
• The relief valve makes sure the pressure cannot damage the system.
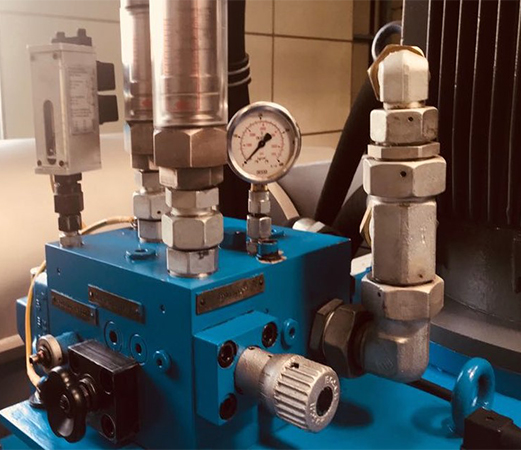
4.Eddy current back-drive (ECB)
The Decanter centrifuge consists from a bowl which rotates at high speed and inner screw conveyor which rotates in the same direction but at lower speed. Wide ranges of slurries can be treated by varying the relative speed of the bowl and the conveyor. An eddy current brake-drive can be used to vary the differential speed by braking the sun-wheel shaft. The brake can be mounted in line with the gearbox or to the side or below the gearbox and be connected to it with belts and pulleys. The braking torque depends on the magnetic flux which in turn depends on the current in the field coil. By changing the current the speed of the brake can be changed and thereby the differential speed.
The current is controlled by a controller, an ABC (Automatic Back drive Controller) or a VS (Variable Speed). The ABC, or VS displays information about set points, main speed, differential speed and torque. The differential speed can either be pre-set to a constant value, or it may be allowed to vary by keeping the torque on the sun-wheel shaft constant. As the name suggests, the ECB can only brake the sun-wheel shaft. The maximum differential speed of the conveyor is therefore limited by the bowl speed, the gearbox ratio and the minimum allowable speed of the ECB.
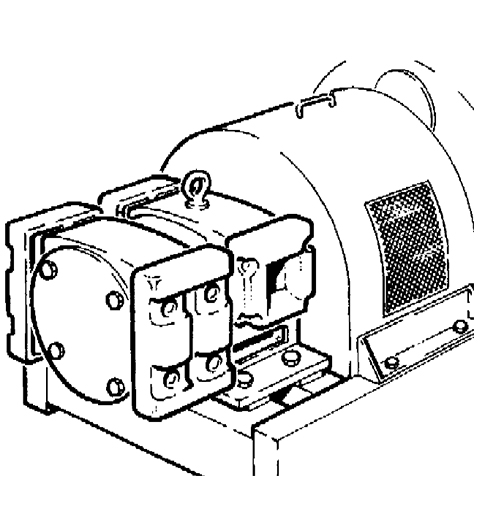