Three Phase Decanter Centrifuge (Tricanter)
n three-phase separation, it is possible to separated two liquid phases from one solid phase at the same time. The Tricanter is the perfect partner for separating these three phases. The different densities of the liquids and the solid mean that all three phases can be discharged simultaneously using the Tricanter. This is the reason for the name Tricanter.
A decanter can not only separate solids from a liquid, but it can also separate two immiscible liquids. A three-phase decanter can discharge two liquid phases and one solids phase. The structure and function of the Tricanter are similar to those of a decanter (two-phase separation). The decisive difference between these two machines concerns the way that the liquid is discharged. The light liquid phase is discharged into the casing through radial holes in the large end hub. The heavy phase is discharged through axial holes in the large end hub.
Three Phase Decanter Centrifuge
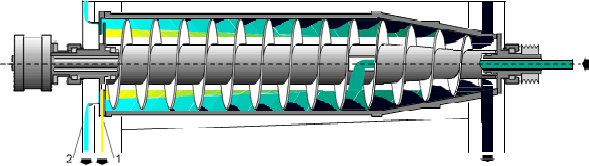
1. Light liquid phase 2. Heavy liquid phase
The liquid radius for the light liquid phase is smaller than the radius for the heavy liquid phase. The liquid level is controlled by plate dams. In order to prevent the light liquid phase from leaving the bowl through the heavy liquid phase outlet, a separating plate is placed on the inside of the large end hub. The heavy liquid phase has to pass under the separating plate before being discharged into the casing. The liquid radius for the heavy liquid phase is controlled by plate dams.
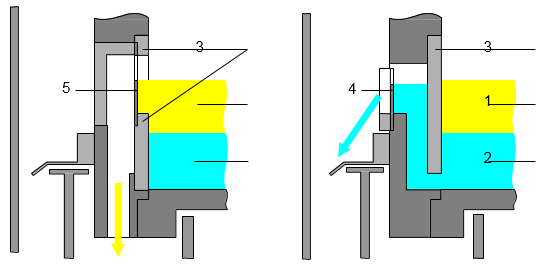
Three phase liquid discharge. Left: Light phase. Right: Heavy phase.
1. Light phase 2. Heavy phase 3. Separating plate
4. Plate dam, heavy phase 5. Plate dam, light phase
The liquid radii for the two phases are to be adjusted in such a way, that the interface level is at a reasonable distance from the light liquid level and from the outer diameter of the separating plate. The interface level can be calculated if the densities of the two liquids are known. The purity of the two liquids can be adjusted by moving the interface level. This is done by changing one (or both) of the liquid levels.
The solids are discharged in the normal way Tricanter - Typical Applications for Three-Phase Separation- Processing of sludges containing oil from refineries, oil ponds, etc.
- Extracting animal/vegetable fats and oils
- Starch manufacture for separating wheat starch and gluten
- Outstanding separation efficiency
- Wide usage in the fish oil and fishmeal field
- Corrosion resistant key parts
- Flexible length-to-diameter model for customized
- Other processing steps/separating stages can be dispensed with, or are no longer required, thereby offering cost savings for the plant owner
- Adaptation to changing conditions (product in the feed) possible at any time
- Automation is possible
- Produced, manufactured and developed in India, for the highest possible production quality in make in India concepts.
- Sealed construction to control odor emissions and avoid contamination of the product
- Ease of operation with continuous or automatic control systems
- Limited consumables such as filter media or filter aids
Compact Design
Base Frame Assembly
The static and dynamic load of machine is high so to sustain that there is use of base frame (22). The rotating assembly is covered with guard (16).
- Wide-ranging performance.
- Performance criteria.
- Five crucial factors determine the performance of decanter centrifuges:
- Centrifugal force required for sedimentation of the solids.
- Clarification area necessary to “capture” the solids.
- Differential speed required to transport the solids out of the decanter.
- Hydrodynamic design, which determines the exact parameters for the turbulence.
- Design of the conveyor and beach sections, which are important for efficient solids transportation.
Characteristic features of centrifuges which meet hygienic requirements are:
- All welds are ground to meet specific sanitary finish standards (optional).
- All product wetted parts are provided with a surface finish in accordance with specified surface roughness values.
- Spray nozzles are provided for the centrifuge housing and for the interior of the scroll body.
- The centrate impeller is adjustable to facilitate the flushing of the bowl.
- Frequency-controlled drives for CIP-cleaning at low speed.
- Electro-polished scroll, housing and bowl surfaces (optional).
Most sizes and models of these centrifuges are available in a variety of rotor and housing seal designs for the following operating conditions:
- Atmospheric
- Vapor-Tight
- Gas-Tight
These centrifuges can also be adapted for operating in closed-loop systems.
Atmospheric Centrifuge
They are used for applications where there is no harm from products or vapors released to the environment.
Lubrication
Decanter centrifuges can be provided with different lubrication systems according to customer requirements. The lubrication system depends on the type of operation, for example, batch or continuous operation and the degree of automation of the entire system. Decanter centrifuge lubrication systems allow for the re-lubrication of rotor bearings during operation.
The availability of the different lubrication systems depends on the centrifuge model. Scroll bearings are lubricated for the entire service life or can be re-greased manually.
Manual Lubrication
Direct lubrication at both rotor bearing blocks via a manual grease pump.
Central Lubrication System
Lubrication from a central manually operated pump. The lubricant is accurately dispensed through a piston distributor to the designated greasing points.
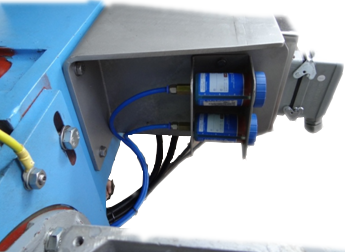
Automatic Grease Lubrication
In contrast to the manual central lubrication system, the greasing system can be operated automatically. This ensures uniform and reliable lubrication of the centrifuge. It prevents bearings from being under or over-lubricated and eliminates short-term spikes in bearing temperatures and excessive grease consumption. The function of the grease pump is controlled by the control system. For the most stringent requirements, an oil-air lubrication system can be provided by additional cost.
Automatic Oil Droplet Lubrication
The fully automatic oil-air lubrication system ensures for minimal quantity lubrication with oil droplets transported via a stream of air to the bearings. Optimal lubrication is achieved at high speeds, with low oil consumption and no loss in performance. Monitoring of the oil and air pressure guarantees high operational safety. Pneumatic designs are available for utilization in explosion-hazardous areas. They are suited for Zone 1 up to temperature class T4 according to ATEX 95.
1. Centrifuge Cleaning
Decanter Centrifuges are usually flushed clean before shutdown. Depending on the application, different cleaning systems may be incorporated into the centrifuge design. Decanter centrifuge are designed for continuous operation and do not have to be opened for cleaning. Decanter centrifuge for pharmaceutical, biotech and food processing applications are designed for the integration into Clean-in-Place (CIP) systems.
2. Cleaning of Centrifuges for Standard Application
For the majority of applications (e.g. waste water, separation of crystalline products), it is sufficient to flush the centrifuge before shutdown through the feed pipe to remove deposits of solids. The flushing time and the type of cleaning fluid are product-dependent. In most cases the use of solids-free centrate will be adequate. Additional rinsing nozzles for cleaning the housing, the bowl exterior and the scroll interior can be installed if requested.
3. Cleaning of Centrifuges for Pharmaceutical, Biotech & Food Processing Application
The requirements for efficient cleaning are particularly high in the biotech, pharmaceutical and food industries. Decanter centrifuge designs its centrifuges to meet the rigid cleaning requirements in these industries.
1. Vibration Monitoring
Vibration sensors transmit acceleration signals to an analyzer that sounds an alarm or shuts the centrifuge down upon reaching the maximum permissible level.

2. Speed & Temperatures Monitoring
SPEED MONITORING
Bowl speed and scroll differential speed are each measured by an inductive proximity switch and shown on a digital display. Continuous monitoring of maximum and minimum values during operation helps to minimize preventable failures and maintain acceptable safety standards.
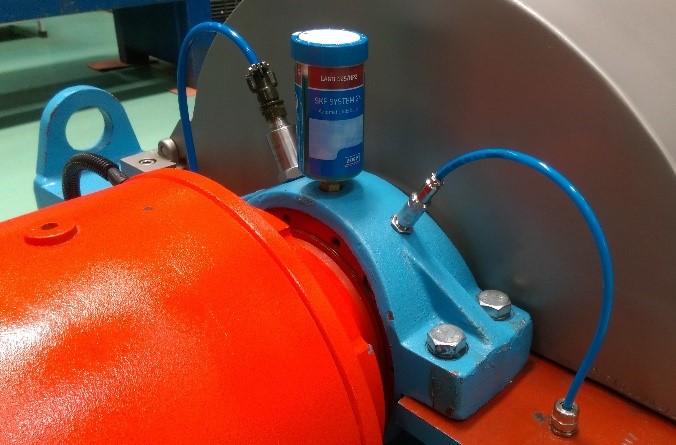
TEMPERATURE MONITORING
Bearing temperatures are continuously monitored on GCF centrifuges by means of resistance thermometers. Upon exceeding pre-set temperature limits – between 100°C and 130°C depending on the individual application - , the centrifuge gives an alarm or shuts down. This preventive measure safeguards against bearing failure or machine damage.
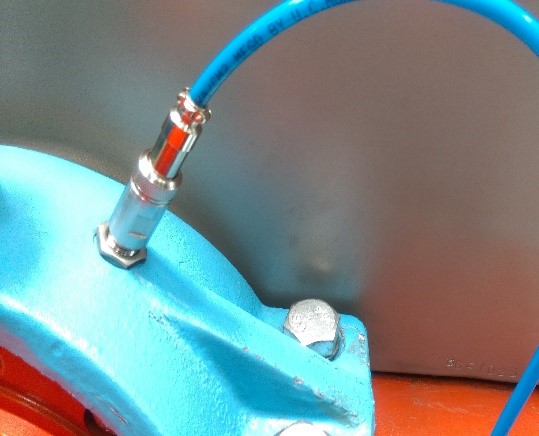
Vapor-Tight Version
Decanter centrifuges are the right choice in cases where substances emitted from the process could pollute the environment of if contact of the product with ambient air is undesirable. Additional seals on rotor shafts and housings provide the necessary seal. Emissions can be eliminated when purge gas/air is applied to seals or when the centrifuge housing is vented.
Gas-Tight Centrifuge
Allow for safe operation with toxic, corrosive or flammable media by applying inert purge gas to rotor seals and by inerting the process chamber and centrifuge housing. Slight positive or negative pressures can be maintained in the process area by regulating the purge gas supply. Special sealing elements minimize the seal gas consumption.