2. The decanter centrifuge is a major item of processing equipment in many industrial applications and illustrates this range of use. The driving forces in the decanter marketplace result almost entirely from the needs of these industrial applications, so their importance to a handbook on the decanter is easy to see. The decanter has no place, however, in domestic, institutional or commercial (business) applications, which are covered by separation equipment of quite different kinds. In addition to reviewing decanter applications by specific industrial end-use, it is necessary first to recognize that there are ways of looking at decanter applications in a more general sense. Mechanical liquid/solid or liquid/liquid separations serve two broad purposes:
1. A utility function, such as the cleaning of cooling water or of a recycled hydraulic fluid; and
2. A process function, such as the recovery of crystallized salt or the polishing of beer.
Utility applications are found throughout the whole of the manufacturing and service industries, and their characteristics are dictated by the nature of the application, and more often than not are independent of the nature of the end-use sector, such as power generation, brewing or the production of pharmaceuticals, in which they are found. Utility applications are. on the whole, of similar levels of importance throughout industry and commerce. Process applications, on the other hand, are usually end-use sector specific, with important variations imposed by operating temperatures and pressures, by the corrosiveness of the liquid or abrasiveness of the solids in the system, and by the individual process needs, such as cake dryness or central clarity. Process applications may be an absolutely vital part of the end-use processor may have only a small part to play.
Decanter applications certainly obey this differentiation. The number of different utility applications is small, although the main one, the dewatering of waste sludges, is an enormous part of the decanter market. The great variety of decanter uses occurs in the very wide range of process applications. This variety of end-use separation applications can be grouped into five broad types: clarification, classification, thickening, dewatering, and washing according to the main purpose of the separation process. It is, of course, very probable that more than one of these may be involved in a particular application. The decanter separates suspended solids (or immiscible liquid droplets) from a liquid stream so that one prime purpose for the decanter is the clarification of this liquid stream as far as possible free from the suspended material. The decanter can be operated so as to give a high degree of clarification, although it is not always possible to achieve high degrees of clarification and of dewatering of the solids at the same time. It is not often that a decanter is used only to clarify a liquid, and it is not by any means the best equipment for clarifying a slurry that contains only a small number of solids in suspension. Waste slurry processing, although not only a clarification process, does require the most effective removal of solids that is possible. In clarification mode, extra efforts must be made to ensure that no cross-contamination between the exit streams is allowed.
The beverage & Food industry is growing continuously, driven by rising population and increasing wealth, shifting consumption patterns, from plain water to juices, tea, wine, beer, and so on. Whether it is wort, pulp, juice, or any other liquid that is extracted, it is essential to ensure high productivity and maintain quality. Decanter centrifuges generally provide both high capacity and short contact time. G-Centri-Force decanter centrifuges are designed for food and beverage applications where good hygiene practices are essential in order to comply with strict sanitary regulations. These decanter centrifuges are available for both 2-phase and 3-phase separation. They are ideal for use in the food industry in situations where the material being processed has to be separated into both a liquid and a solids phase, or into two liquid phases and a solids phase. The BF series range provides the most cost-effective, high-performance solution combined with the lowest power consumption and life-cycle costs available within the process industries., with both very low (<1%DS>) and very high solids contents. Whether you require lower life-cycle costs, higher cake dryness driven by 3 stages planetary gearbox. G-Centri-Force decanter centrifuges provide design options such as grooves in the bowl to provide a more hygienic way to transport the material being processed through the unit. Other options include a parking disc and a complete purge system to keep foaming to a minimum and limit oxidation; pulp wash facilities; process rinse and a full cleaning-in-place (CIP) capability, as well as FDA-approved elastomers and seals.
The processing of fruits and vegetable material includes a number of operations where the decanter has a part to play. This includes:
1. The extraction of oils from seeds, such as rape. corn (maize), cottonseed. sunflower, safflower, groundnut (peanut), flax (linseed), castor, Tung, soybean, and sesame:
2. The extraction of oils from fruits such as olive, palm (and palm kernel) and coconut:
3. The extraction of starch from corn (maize), wheat, tapioca, and potatoes:
4. The separation of gluten from starch; and
5. The canning of whole or cut fruit and vegetables.
The G-Centri-Force Decanter centrifuge meets your requirements and helps to ensure your success:
1. Excellent performance due to optimized speed and separation area arrangement
2. Top yield thanks to the special extraction device
3. Good clarification performance due to patented scroll design
4. Low maintenance cost and easy operating as a result of highly functional concept
5. Low oxygen pick-up due to short residence time
6. Optimum product quality thanks to special feed chamber, assuring gentle treatment
7. Minimized energy consumption as a result of the energy recovery system
8. Long service life due to robust design and high-grade materials
9. Maximum availability as a result of excellent cleaning properties and fully automated CIP
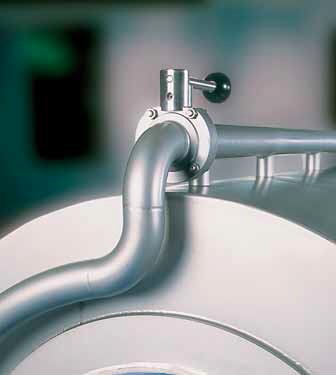
CIP Systems in G series Decanters
The Graphic Presentation of the cleaning procedure is meant as a suggestion, different processes will require specific cleaning cycles. Lye detergents and other cleaning agents used for cleaning already existing stainless-steel plant parts are normally also applicable in the wash cycles for the BF Series decanters. Separate, automated CIP stations are available on request if there is no possibility to connect to already existing systems. The procedure for cleaning in place (CIP) can be divided into two parts. High-speed CIP while the decanter is running at production speed, and low-speed CIP while the decanter is running with a speed corresponding to approximately 1-G force. The cleaning liquid, temperature and time that are necessary for cleaning, depend in detail very much on the application. The different steps are only indicated. The time should be adjusted to suit actual operating conditions.
High speed CIP
The cleaning liquid is fed through the feed tube and through the spray nozzles. Most solids inside the bowl are washed out, and the outside of the bowl and the casing are cleaned.
Low speed CIP
The low-speed CIP is obtained by driving the main drive motor by a small frequency converter set at a low frequency so that the bowl speed corresponds to approximately 1 G at the inside periphery of the bowl. As the bowl rotates at low speed and also alternating in direction, the liquid introduced during these CIP cycles will become turbulent in the bowl giving a tumbling effect like the one seen in a washing machine. The cleaning liquid is fed through the feed tube, and parts, like the conveyor body that are not cleaned during high-speed CIP, will be cleaned. Spray nozzles are not used during low-speed CIP.
As low-speed CIP may discharge solids out of the bowl and into the discharge chute of the casing, it is often used to finally run the decanter up to high speed and flush with the spray nozzles.
Flushing capacity to the decanter and the spray nozzles during CIP depends on the decanter type and size as well as on the application. The pressure to the spray nozzles should be approx. 2 bar.
The wash cycles may continue until the bowl is adequately cleaned. Wash solutions may be recycled back to the bowl in order to save detergent, caustic solutions, and other agents. It is recommended to install a filter if recycling is used as nozzles may otherwise clog. Cleaning in place systems may be fully automated and interlocked with the centrifuge control system.
It must be noted that a CIP program can vary a lot depending on the application and actual conditions. It is, therefore, necessary to test and adjust the CIP program after installation of the decanter, in order to find a suitable combination between cleaning liquid, capacity, temperature and time.
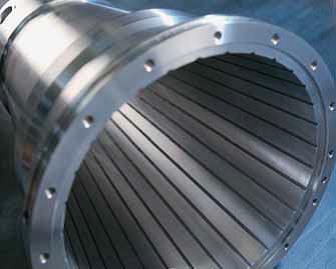
Bowl With Grooved
A sanitary machine is a machine which will be clean after normal operating conditions (followed by CIP) without dismantling. Sanitary machines must be used when the possibility exists of bacteriological or fungicidal growth on uncleaned material having an adverse effect on the product being processed. This would normally be relevant to dairy, other food or pharmaceutical applications.
The following points show where a sanitary decanter may differ from an ordinary decanter.
1. Internal bowl surface is plain or grooved.
2. Joints between bowl sections sealed with O-rings. Hexagon head screws.
3. No sharp corners in bowl or casing. Feed pipe - internally polished.
4. Conveyor flights polished - no hard surfacing.
5. Feed inlet in conveyor ground and polished before conveyor flights are fitted. All welded seams in the casing and the conveyor are ground and polished.
6. Spray nozzles for rinsing the inside of the casing and solids discharge zone. Specially designed gasket between the cover and the bottom part of the casing. Food grade grease for bearings.
7. Cleaning in place system with frequency converter drive main drive motor for low-speed CIP.