Liquid Discharge Section
In a two-phase decanter, the liquid level is regulated by dam plates. When operating in a three-phase mode, each phase discharges over a set of dam plates into separate baffled compartments in the casing. In certain applications, a centripetal pump discharge that utilizes the pressure head developed by the rotating liquid phase is used to pump the liquid from the decanter.
Decanter centrifuge offers a wide range of wear protection to meet the requirements of the many different applications in which centrifuges are installed:
- Welded hard facing or spray coating
- Ceramic
- Tungsten carbide tiles
- Chilled hard metal port castings
- Plastic liners
In order to minimize maintenance costs for applications involving highly abrasive products, all wear protection elements, except welded hard facings or spray coatings, are field replaceable.
1. Wear Protection Hard-Surfacing Conveyor
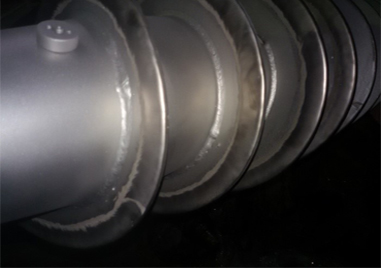
2. Wear Protection Tiled Conveyor
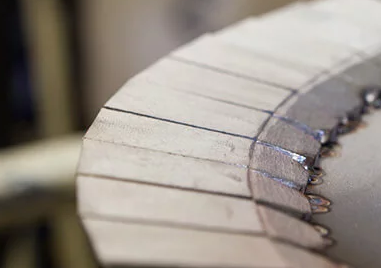
Most decanter centrifuge comes with moon types of plate dam, but some of the application decanter centrifuges have pressurized discharge of the liquid phase by use of a paring disc, or centripetal pump. The clarified liquid enters the paring chamber. The stationary paring disc which has channels for the liquid is immersed in the rotating liquid. This causes a pressure differential and the liquid is forced through the channels converting the energy of rotation into a pressure head sufficient to pump the liquid out of the machine and to succeeding processing steps.
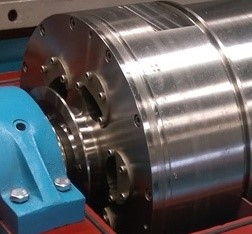
Decanter With dam plate
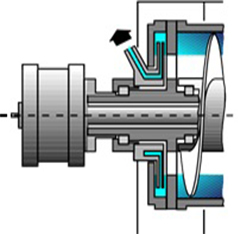
Decanter with paring Disc
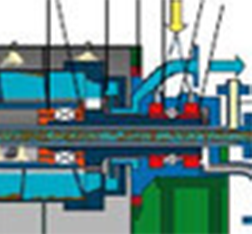
Decanter with Centripetal pump
By applying back pressure to the paring disc outlet, it is possible to minimize or even eliminate air (oxygen) pick-up and foaming.
Paring discs may also be made as so-called friction (or vaneless) paring discs.
Instead of channels the paring disc consists of two discs at a small distance, 2 to 4 mm. This type of paring disc is softer to the liquid, but has lower capacity and higher power consumption than the type with channels.